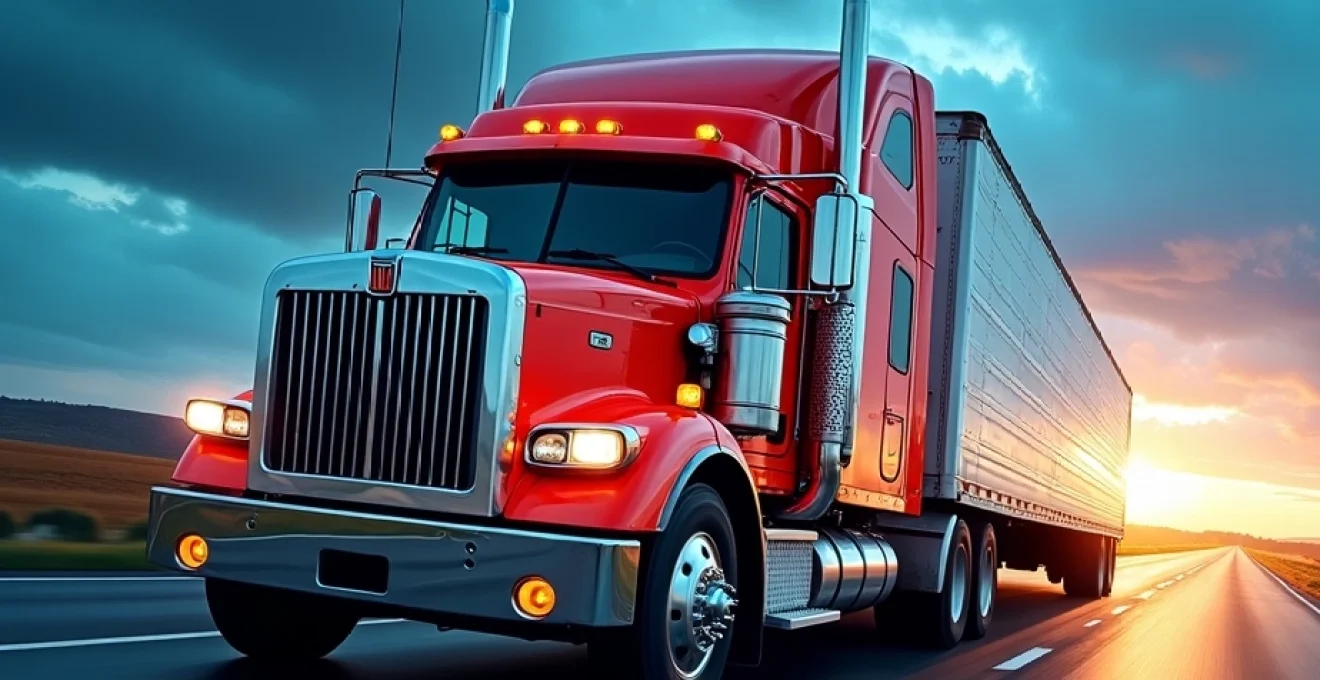
Trucks are the backbone of the transportation sector, and their operational reliability is crucial for keeping the wheels of business turning. Regular maintenance and repairs are not just a cost, but an investment in the vehicle's lifespan and performance. By prioritizing routine service and promptly addressing issues, truck owners and operators can avoid costly downtime and serious mechanical failures. Let's explore how proactive maintenance can ensure your truck fleet stays in top condition, and how modern technology is revolutionizing the way we approach truck maintenance.
Critical Components for Truck Maintenance
To maintain optimal performance and safety, there are several key components in a truck that require special attention. The engine is, of course, the heart of the vehicle, and regular oil changes are crucial to protect it from wear and tear. The quality and condition of the oil are directly linked to the engine's lifespan and efficiency. The braking system is another critical component that should never be ignored. Worn brake pads or rotors can not only reduce braking performance but also lead to damage to other parts of the braking system.
The tires are the truck's contact point with the road, and their condition affects both safety and fuel economy. Regular checking of tire pressure and wear is essential. The transmission, which transfers power from the engine to the wheels, is also a vital component that requires regular inspection. Neglecting transmission fluids or adjustments can lead to costly repairs or complete failure.
Electrical systems, including the battery, alternator, and starter motor, play an increasingly important role in modern trucks. These components must be inspected regularly to avoid unexpected failures. Finally, but not least, the cooling system is critical to maintaining optimal engine temperature. A well-functioning cooling system prevents overheating and helps to extend the engine's lifespan significantly.
Proactive maintenance of critical components is not just a cost, but an investment in the truck's long-term reliability and performance.
Time-Saving Diagnostic Tools for Truck Mechanics
In today's rapidly evolving technological landscape, truck mechanics have access to a range of advanced diagnostic tools that drastically reduce the time it takes to identify and resolve problems. These tools enable more precise diagnoses, resulting in faster repairs and reduced vehicle downtime. Let's take a closer look at some of the most effective diagnostic tools that modern truck mechanics use.
OBD-II Scanners for Quick Fault Code Analysis
OBD-II scanners (On-Board Diagnostics II) are indispensable tools for any truck mechanic. These devices connect to the truck's diagnostic connector and provide immediate access to the vehicle's fault codes. By interpreting these codes, mechanics can quickly identify specific problems without time-consuming manual troubleshooting. Modern OBD-II scanners can also monitor real-time data from various sensors, providing valuable insights into the vehicle's performance under various conditions.
Digital Multimeters for Electrical System Checks
Digital multimeters are essential for diagnosing electrical problems in trucks. These tools measure voltage, current, and resistance in electrical circuits, and are essential for identifying short circuits, poor connections, or failing components. With the increasing complexity of modern truck electrical systems, precise measurements are critical for effective troubleshooting and repair.
Thermal Cameras for Detecting Overheating
Thermal cameras have become an increasingly popular tool among truck mechanics. These devices visualize the heat distribution in various components, making it possible to detect overheating or abnormal heat development before it leads to serious problems. Thermal cameras are particularly useful for identifying problems in engines, braking systems, and electrical components that would otherwise be difficult to detect visually.
Compression Gauges for Engine Performance Diagnostics
Compression gauges are indispensable for assessing the engine's internal condition. By measuring the compression in each cylinder, mechanics can quickly determine if there are problems with valves, piston rings, or cylinder walls. This tool is particularly useful for diagnosing performance loss or uneven engine operation and can save significant time in the troubleshooting process.
The use of these advanced diagnostic tools has revolutionized the way truck mechanics work. They not only enable faster and more precise diagnoses, but also help to reduce misdiagnoses and unnecessary repairs. This results in shorter workshop stays for the trucks and increased efficiency for the transport companies.
Preventive Maintenance Plans for Long-Haul Transport
Implementing an effective preventive maintenance plan is crucial to ensuring the reliability and longevity of trucks in long-haul transport. A well-structured plan can prevent unexpected breakdowns, reduce operating costs, and maximize vehicle uptime. Let's take a closer look at some key elements of a comprehensive preventive maintenance plan for trucks.
Regular Oil Changes with Synthetic Oil for Increased Engine Life
Regular oil changes are fundamental to engine health and performance. For trucks in long-haul transport, it is recommended to use synthetic oil, which provides better protection under extreme conditions and during long operating periods. Synthetic oil has better resistance to degradation and can maintain its lubricating properties over a longer period. It is recommended to follow the manufacturer's recommendations for oil change intervals, but for heavy trucks in long-haul transport, this can typically be every 20,000 to 30,000 kilometers.
Tire Rotation and Balancing for Optimal Wear
Regular tire rotation and balancing are critical to ensure even wear and maximize tire life. For trucks in long-haul transport, this should be performed every 20,000 to 30,000 kilometers. Proper tire maintenance not only improves safety but also contributes to better fuel economy and driver comfort. It is also important to check the tire pressure weekly, as the correct pressure reduces wear and improves fuel consumption.
Air Filter Replacement for Improved Fuel Economy
A clean air filter is essential for optimal engine performance and fuel economy. For trucks that often operate in dusty or polluted environments, more frequent air filter changes may be necessary. A clogged air filter can significantly reduce engine efficiency and increase fuel consumption. It is recommended to inspect the air filter at each oil change and replace it according to the manufacturer's recommendations or earlier if it is visibly dirty.
Brake System Inspection and Service
Regular inspection and maintenance of the brake system are critical for safety in long-haul transport. This includes checking brake pads, rotors, drums, and brake fluid. For heavy trucks, a thorough brake inspection should be performed every 20,000 to 30,000 kilometers, or more often under demanding operating conditions. It is also important to adjust the brakes regularly to ensure even and efficient braking on all wheels.
By implementing these preventive maintenance measures, truck owners and operators can significantly reduce the risk of unexpected breakdowns and costly repairs. A proactive approach to maintenance not only ensures vehicle reliability and safety but also helps to optimize operating costs and extend the truck's lifespan.
Cost-Effective Repair Strategies for Fleet Owners
For fleet owners, balancing maintenance costs and operational efficiency is a constant challenge. However, implementing cost-effective repair strategies can help reduce expenses without compromising on quality or safety. A key strategy is to invest in preventive maintenance, which in the long run can save significant sums by preventing major breakdowns.
Another effective approach is to establish an in-house workshop for routine maintenance and minor repairs. This can reduce dependence on external workshops and provide better control over maintenance costs. For fleets of a certain size, the investment in their own workshop and personnel training can quickly pay for itself through reduced service costs and minimized downtime.
Standardizing the fleet is another strategy that can provide significant cost savings. By limiting the number of different truck models and brands in the fleet, one can reduce the need for a wide range of spare parts and specialized training. This simplifies maintenance routines and can lead to more efficient inventory management of spare parts.
Investments in diagnostic equipment and training of mechanics in the latest technologies can ultimately lead to significant savings through faster and more precise fault diagnosis.
Implementing a robust fleet management system is also crucial for cost-effective maintenance. Such systems can track maintenance history, schedule preventive maintenance, and identify vehicles that require additional attention based on performance data. This enables a more proactive approach to fleet maintenance, which can reduce the number of unexpected repairs and maximize vehicle uptime.
Modern Technologies for Predictive Truck Maintenance
The rapid development in technology has led to a revolution in the way truck maintenance is performed. Predictive maintenance, which uses advanced technologies to predict when maintenance is needed, is becoming increasingly prevalent in the transport industry. This approach can significantly reduce downtime and maintenance costs by identifying potential problems before they develop into serious failures.
IoT Sensors for Real-Time Vehicle Status Monitoring
Internet of Things (IoT) sensors installed in trucks provide continuous monitoring of critical components. These sensors can measure everything from engine temperature and oil pressure to tire pressure and brake wear. By collecting data in real-time, these sensors can provide early warnings of potential problems, enabling proactive maintenance planning. For example, a gradual increase in engine temperature may indicate the need for cooling system service before a serious problem occurs.
AI-Powered Analytics Tools for Maintenance Forecasting
Artificial intelligence (AI) and machine learning have become powerful tools in predictive maintenance. These technologies can analyze vast amounts of data from IoT sensors and historical maintenance records to identify patterns and predict when components are likely to fail. AI-powered systems can also optimize maintenance plans by taking into account factors such as driving conditions, load, and route to determine the most effective time for service.
Telematics Systems for Fleet Management and Maintenance Planning
Telematics systems integrate GPS tracking, communication, and vehicle diagnostics to provide a comprehensive overview of fleet performance and maintenance needs. These systems can automatically schedule maintenance based on vehicle usage and performance data, ensuring that each vehicle is serviced when needed, neither too early nor too late. Telematics also enables remote monitoring of vehicle status, which can be particularly valuable for managing problems that arise during long-distance transport.
The implementation of these modern technologies for predictive maintenance can provide significant cost savings for fleet owners. By identifying potential problems before they develop into costly breakdowns, one can reduce downtime and optimize maintenance planning. This results not only in reduced repair costs but also in increased operational reliability and efficiency for the entire fleet.
Environmentally Friendly Maintenance Practices for Truck Operators
In an era of increased focus on environmental protection and sustainability, it is important for truck operators to implement environmentally friendly maintenance practices. These practices can not only reduce environmental impact but also lead to cost savings and improved reputation. By adopting green maintenance routines, truck operators can help reduce the carbon footprint in the transport sector while maintaining high performance and reliability in their fleet.
One of the most effective environmentally friendly practices is to implement a strict preventive maintenance program. This ensures that trucks operate at optimal efficiency, which reduces fuel consumption and emissions. Regular checking and adjustment of engine settings, for example, can significantly improve fuel economy. Likewise, proper tire maintenance, including regular checking of tire pressure and wheel alignment, can reduce rolling resistance and thus fuel consumption.
The use of environmentally friendly lubricants and coolants is another important practice. Biodegradable oils and antifreezes reduce the risk of environmental damage in the event of leaks or spills. Many of these products also have a longer lifespan, which reduces the need for frequent replacements and thus minimizes waste production.
Investing in modern, low-emission technology for truck maintenance can have a significant positive environmental impact over time.
Recycling and proper disposal of used parts and fluids are also critical. Establishing a comprehensive recycling program for everything from used oil filters to worn tires can significantly reduce the waste sent to landfills. Many components, such as batteries and catalysts, contain valuable materials that can be recycled and reused.
Implementing water-saving techniques in washing processes is another environmentally friendly practice. The use of water-efficient washing systems and reuse of wash water can drastically reduce water consumption. Some advanced systems can reuse up to 80% of the wash water, which not only saves water but also reduces the costs associated with water consumption and wastewater management.
Finally, training personnel in environmentally friendly maintenance practices is essential. This includes training in the proper handling and disposal of hazardous materials, efficient use of resources, and awareness of the environmental impact of various maintenance activities. By creating a culture of environmental awareness among maintenance personnel, truck operators can ensure that environmentally friendly practices become an integral part of the daily operation.